MIT simplifies 3D printing by making it easier to modify 3D models
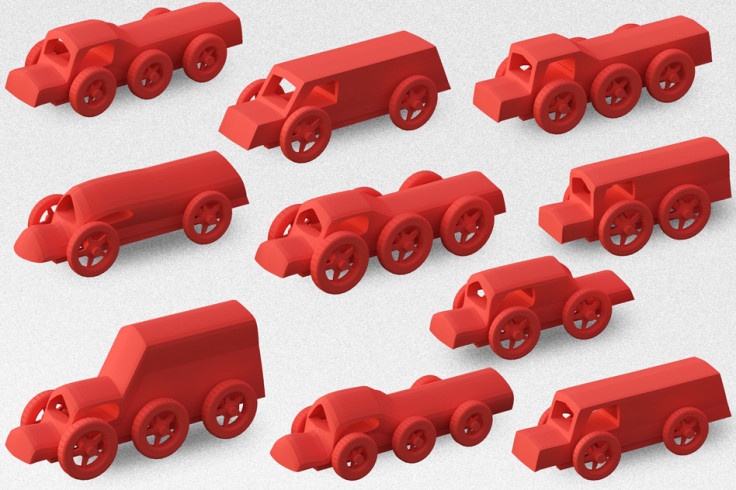
MIT has invented a new web-based software that makes it much simpler for users to make modifications to 3D models they would like to print out on 3D printers. The software has the ability to cut down CAD geometry calculations from hours down to minutes.
3D printing, also known as additive manufacturing, is becoming increasingly popular with consumers, but it is currently a very fiddly process that is not really easy enough for consumers. In order to 3D print items, a user needs to start by designing a 3D model in Computer-Assisted Design (CAD) software.
CAD software is most commonly used by product designers, engineers and computer animators, who all have specialised knowledge of the tools, and creating 3D models is an intricate and time-consuming process even for them.
However, even after the design is complete, it might not print out properly on a 3D printer, and has to be tested on simulation software. Testing out a 3D model design to see if it will print out properly can take several hours of tests, and every time the design is changed, the tests have to be run again.
For this reason, consumer 3D printing largely involves accessing online repositories of prefabricated 3D models, pre-tested and converted from CAD file data, and even then, often the models do not work, as IBTimes UK discovered when we reviewed the Robox 3D printer.
Speeding up CAD to 3D printer tests
Seasoned users of CAD software and 3D printers often use the advanced settings these software offer to manually change numerical parameters of an object and calculate resulting geometries, then store them to a database for future use, but this is not an efficient process.
To solve this problem, MIT and the Interdisciplinary Center Herzliya (IDC Herzliya) in Israel teamed up and decided to run all the usual CAD to 3D printer simulation tests in the cloud. They have developed a web-based interface called Fab Forms that allows users to quickly modify a CAD design's parameters and instantly view a visual representation of the model using slider buttons.
"We envision a world where everything you buy can potentially be customised, and technologies such as 3-D printing promise that that might be cost-effective," said Masha Shugrina, an MIT graduate student in computer science and engineering and co-designer of the new system.
"So the question we set out to answer was, 'How do you actually allow people to modify digital designs in a way that keeps them functional?'"
Autodesk wants to develop software further
So let us say a user is trying to 3D print out a high-heeled shoe, and he or she wants to change the height of the object or width of the base. To save users from creating a design that is unstable or unfeasible, the software has been programmed to remove all parameter values that do not work and stick to geometries stored in the database, so the user can only move the sliders to alter the design in a way that will print out properly.
However, the user might want to change the value of a parameter to a geometry not stored in the database, so instead, the software sends calculations of the new dimensions to be computed by several servers in the cloud, which takes minutes, rather than hours.
The researchers from MIT and IDC Herzliya presented their paper on the Fab Forms system at the Association for Computing Machinery's Siggraph conference in August, and MIT says that leading 3D modelling software firm Autodesk was interested in getting involved, as the firm had been separately investigating the same problem under their Project Shapeshifter.
"We have a thing called Project Shapeshifter that is very similar to what a lot of other people are doing right now, which is making these geometry generators that have a parametric model you can explore," said Ryan Schmidt, a senior principal research scientist and head of the Design and Fabrication Group at Autodesk Research.
"But they all have this common problem: that you can very easily make something that won't work on your printer. What I thought was super-exciting about this work is that it can prevent you from designing something that isn't going to print or that isn't going to be strong enough once you've printed it."
© Copyright IBTimes 2024. All rights reserved.