The Strati: World's First 3D-Printed Electric Car Built in Just 44 Hours
It's been a really exciting year for 3D-printing, what with the technology being used in medical breakthroughs to save lives in Spain, to print multiple houses in China and to build an entire castle in a back garden in the US.
And now we have a new first to add to the list in the 3D-printing industry – the world's first electric car built from 3D-printed parts.
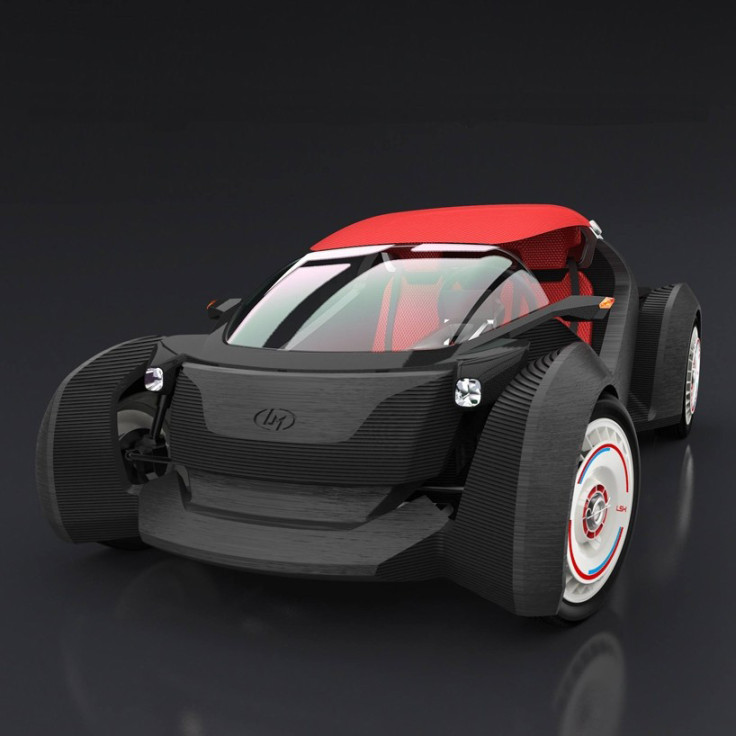
The Strati, a project by Arizona-based Local Motors, was constructed in a record 44 hours at the International Manufacturing Technology Show in Chicago last week, where visitors could watch the car being printed and assembled live.
The car is based on a design by Michelle Anoe of Turin, Italy, who won an online competition to design how the Local Motors prototype vehicle would look out of over 200 entries in June.
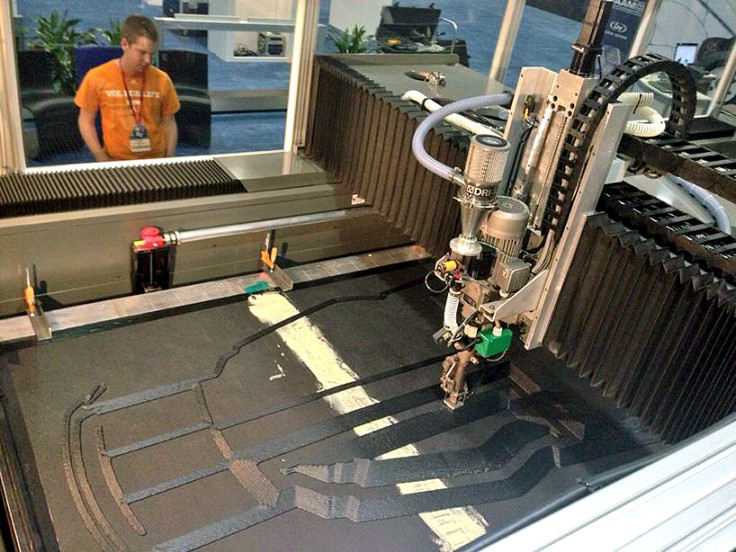
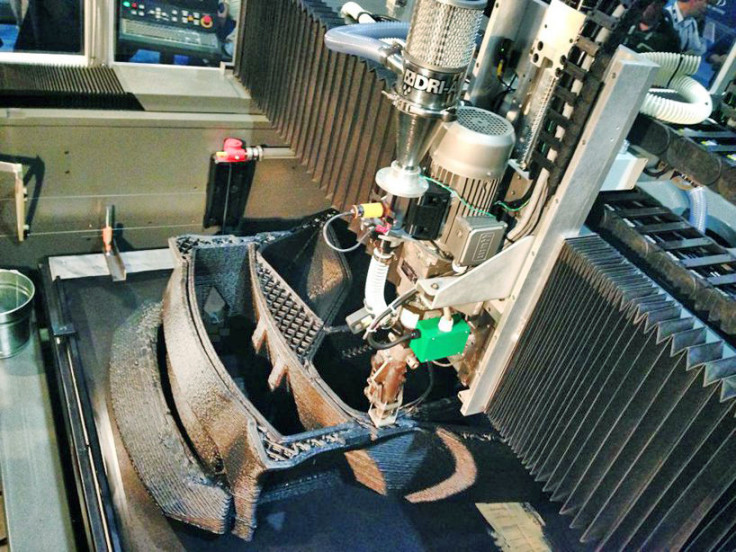
The Strati is not the first car ever to be 3D-printed – that honour goes to the Urbee 2, which took 2,500 hours to make last year.
However what makes this car interesting is that the whole vehicle is only composed of a total of 40 parts.
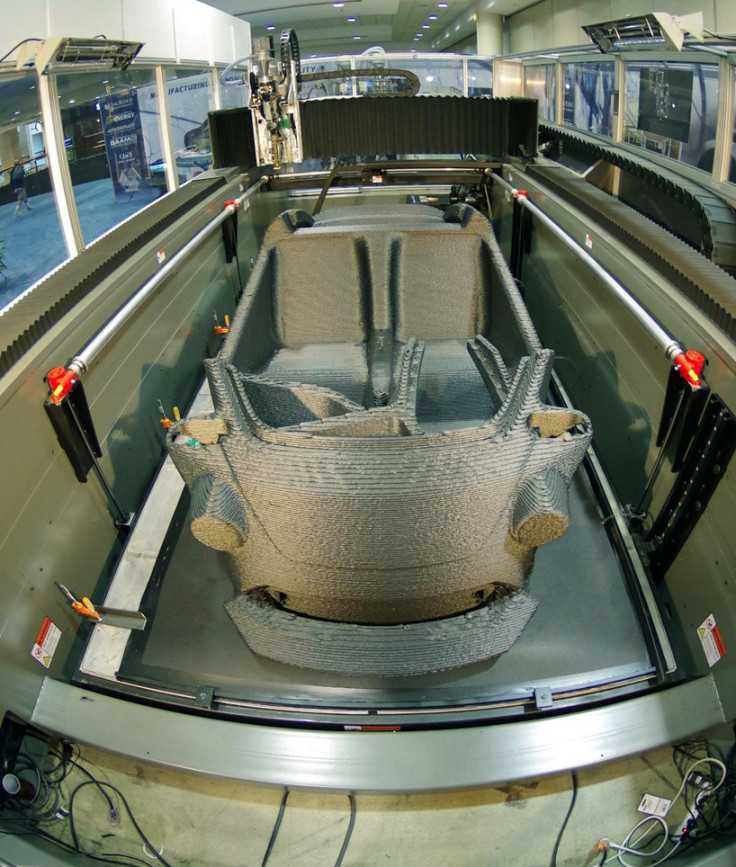
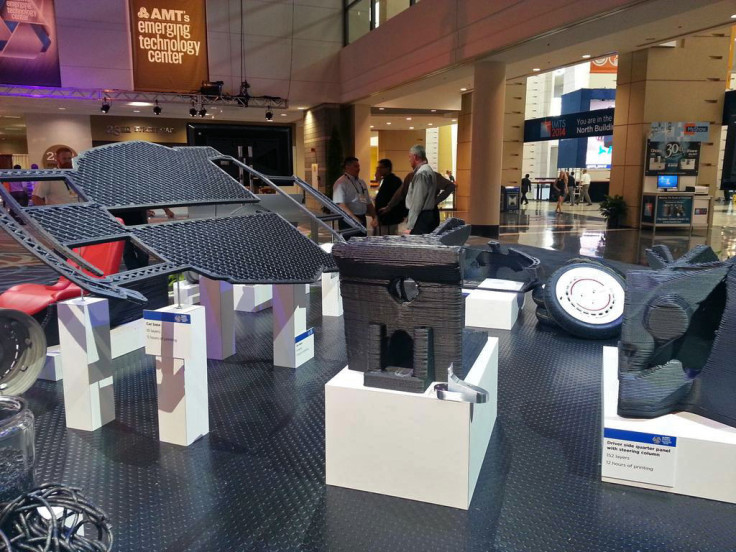
Apart from the car's drivetrain, suspension, battery, tires, wheels, wiring, electric motor and windshield, (much of which come from a Renault Twizy electric car or are made using conventional manufacturing methods), the rest of the car including its chassis, dashboard, seats and body is 3D-printed from carbon fibre-reinforced thermoplastic.
The Strati has a top speed of 40mph and its battery lasts for between 120 and 150 miles.
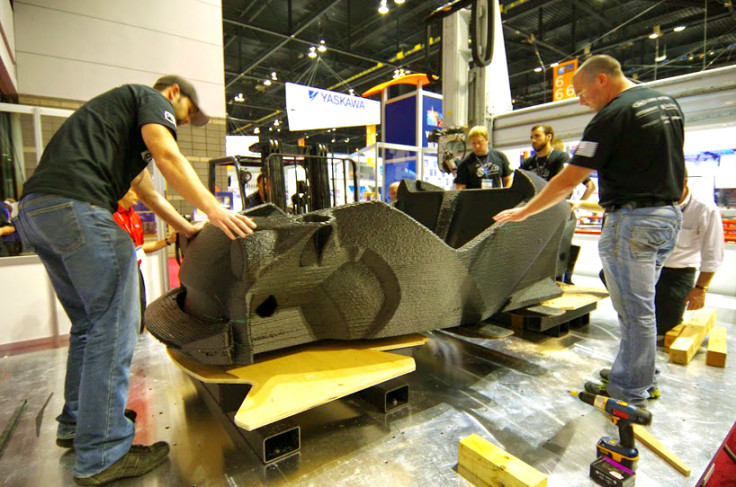
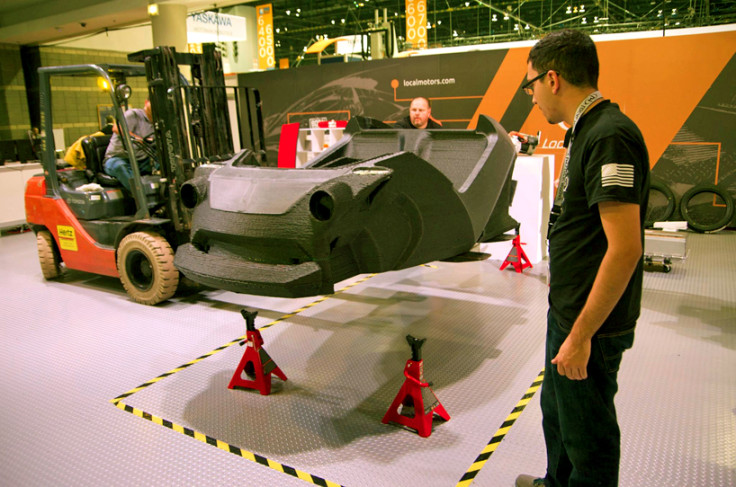
The technology behind the car, however, is based on research conducted by Local Motors together with Oak Ridge National Laboratory, the Association for Manufacturing Technology (AMT) and metal fabrication equipment makers Cincinnati Inc.
The four organisations are trying to revolutionise how cars are made, in order to bring costs of manufacturing down, lower vehicle weight and speed up product delivery.

"We made the first in May and drove it in June. It drove marvellously, much better than I expected," Local Motors' engineer James Earle told USA Today.
"One of the surprises was how quiet it is. There's no sound from the frame, because it's all one piece of carbon fibre."
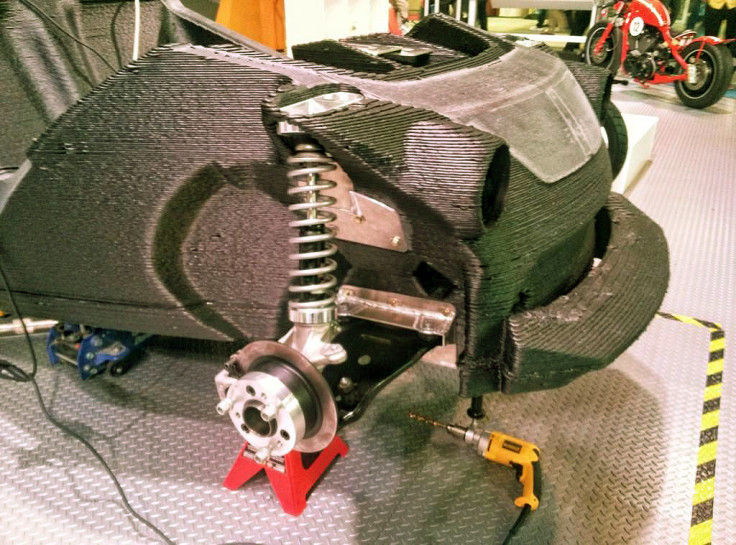
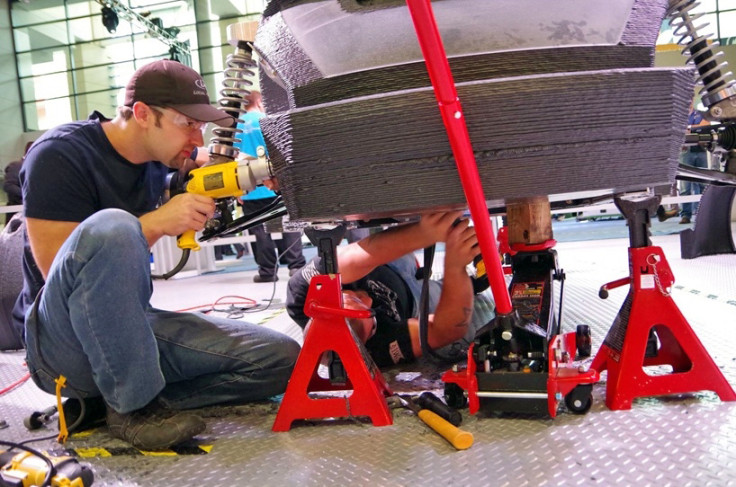
Cincinnati Inc supplied the Big Area Additive Manufacturing (BAAM) 3D printer which is able to print parts measuring 3ft x 5ft x 10ft.
"The BAAM machine can be used for actual production. The deposition rate of 40 pounds per hour of carbon reinforced ABS plastic and the large size mean that large parts, like a car, can be produced using additive technology," said Andrew Jamison, CEO of Cincinnati Inc.
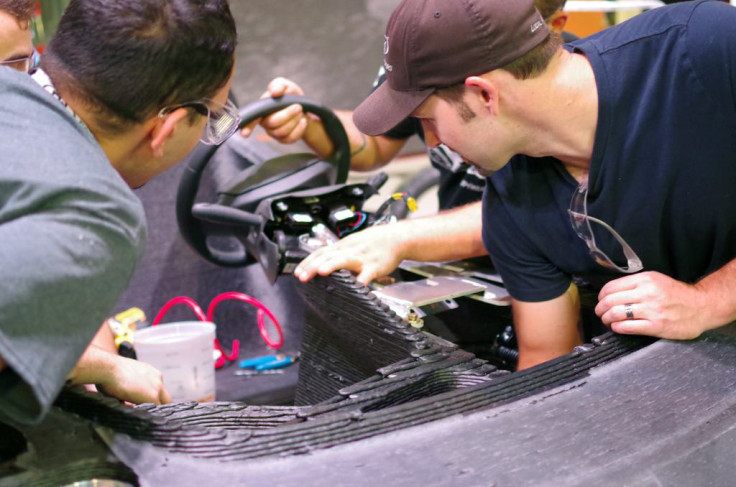
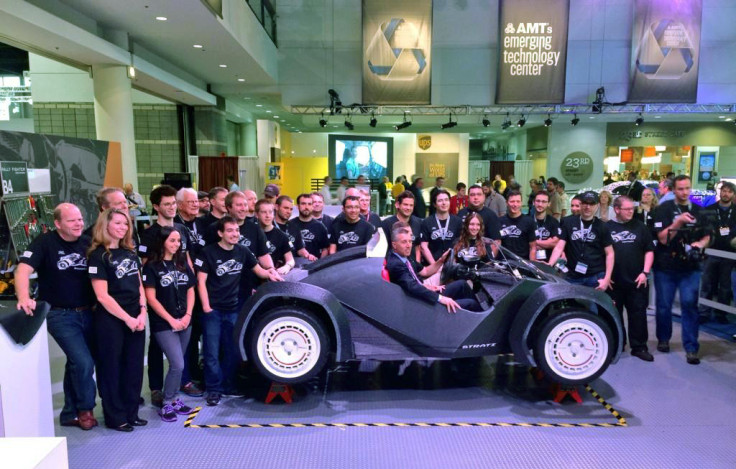
After now having made three 3D-printed electric cars successfully, Local Motors now hopes to produce 3D-printed automobiles retailing between $18,000 to $30,000 (£11,000 to £18,000) with the option to add customised features.
Even better, Local Motors will now integrate 3D-modelling software firm Autodesk's Spark Platform into the car-printing production process to streamline the process further.
Local Motors' CEO John B Rogers, Jr said: "This brand-new process disrupts the manufacturing status quo, changes the consumer experience and proves that a car can be born in an entirely different way."
© Copyright IBTimes 2025. All rights reserved.