How English Willow From UK Forests Drive India's $12 Million Cricket Bat Industry
English willow bats can cost up to $1,000
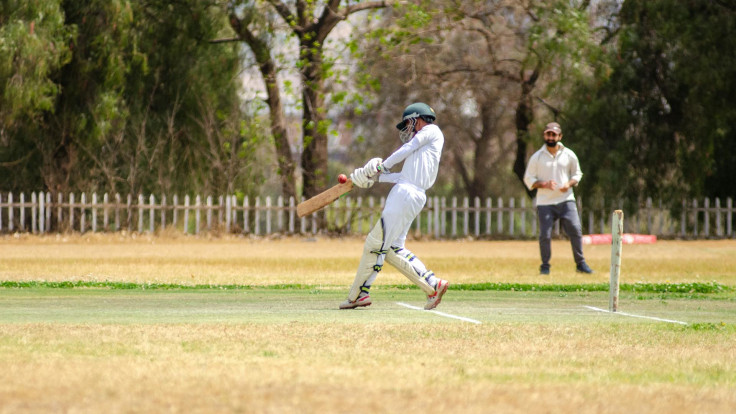
Cricket is a sport that runs wild in almost every street in India, with people from all walks of society playing or watching it passionately. People spend hours in shops trying to find the best quality cricket bat, meticulously checking the "ping" and ensuring it's "knocked in" well for use in the streets or a professional cricket match.
Certified cricket bat makers like Sareen Sports (SS) in India are among the top manufacturers in the world. Pro players in regional tournaments and at the national level use their bats, which are known for their high performance and quality and can cost up to $1,000. While making a cricket bat is labour-intensive, the high price is due to the unique wood used to make these highest-quality bats.
The willow is shipped halfway across the world to India from the UK. A forest in England's Chelmsford is world-renowned for the English willow. Since the 1800s, JS Wright & Sons, an English willow tree supplier, carefully sources wood from the region and readies it for shipping to bat manufacturers. The company supplies 75% of the willow for the world's cricket bats.
What is Special About English Willow?
English willow cricket bats are durable, lightweight, and known for their superior quality. Most professional players prefer the tight-grained willow as more compact wood offers high performance right from the start. However, growing these trees and developing the best quality wood to create top-grade cricket bats is a process that can take up to 15 years. It requires an experienced eye and regular inspection to ensure the willow grows slowly to produce a uniform, tight-grained composition.
The ideal tree for a cricket bat grows straight and slow, resulting in more grains packed closely in the wood. A fast-growing English willow tree will have fewer and broader grains, and bats made from these will be lighter and softer, requiring them to be played with for a while or "knocked in" to harden the face of the bat. In simple terms, the more complex the bat, the further the player can hit the ball.
Sourcing and Preparing English Willow
JS Wright & Sons director Oliver Wright spends much time outdoors, monitoring trees ready to be turned into cricket bats. When he comes across an English willow tree that is 60 inches in diameter, he inspects it before bringing it down. Simultaneously, side shoots on these trees are trimmed yearly to prevent knots from appearing in the wood.
There are several risks, though. The dangers of rotting due to too much access to water or a ruined bark due to pests and insects are regular problems. When a tree is ready, the company aims to carve as many bats as possible. Firstly, the logs are cross-cut into 28-inch pieces, then split into smaller slices called clefts, eventually becoming a cricket bat.
In an interview with Business Insider, company director Jeremy Ruggles said that the average number of bats made from a single tree is 40. However, he highlighted that the current record is 700 bats out of a single tree. The tricky part of the job is identifying the face of the cleft, the part where the ball strikes the bats. Choosing the best side of the cleft as the face of the bat is crucial since customers pay close attention to this cross-section when buying them. Ruggles said you want the straightest grain, less colour, and no knots, adding that whichever side looks nicer is chosen as the face of the bat.
Once the face of the bat is identified and marked, both ends of the cleft are covered in a special petroleum-based wax, just 10 millimetres, to reduce splitting. Before they are shipped, the last step is grading the notches on a scale between 1 and 20, with one being the best. Bruce Arthy does the initial grading and has worked with the company for 48 years. Once graded based on the wood quality and appearance, the sorted clefts are stacked in the open air and then in a kiln to remove any moisture. This process can't be rushed, as it can result in splits or heavy clefts.
JS Wright & Sons ships graded clefts all over the world. It has supplied Sareen Sports in Meerut, India, for nearly half a century.
From Clefts to World-Class Cricket Bats at SS
Sareen Sports manufactures from 500 to 800 bats daily using the processed clefts it receives from JS Wright. Turning a cleft into a bat takes 24 to 36 hours from start to finish. The process starts by smoothing out the clefts and cutting them down to the standard size, then carving a V-shape into one end using a band saw for the handle to be glued in.
The handle is made from cane imported from Singapore and has layers of rubber inside for shock absorption. The cane is smoothed out and glued into the cleft cavity, which takes around 16 hours to dry. As the bat starts to take shape, workers use basic tools like a planer to fine-tune it and make it more lightweight. A cricket bat's face is flat and curved at the back, making it thicker at the centre, exactly where it'll contact the ball, also called the "sweet spot."
The next crucial step involves a mechanical process of further compressing the face to harden the wood grain since the English willow is soft in its raw form. The workers finish the glued handle by tightly winding a string around it and inserting a rubber grip before the bats are sanded and polished for sale.
Rising Counterfeits and Risks of Willow Shortage
Counterfeiters often use cheaper wood like Indian Kashmir willow and try to pass it off as English willow, a practice the Indian police have been cracking down on for years. One way to spot a bat made from Kashmir willow is that they are heavier than English willow and typically more yellowish-brown. Managing director of Sareer Sports, Jatin Sareen, says purchasing from a certified dealer is the best way to get a legit bat.
While Jatin's business is booming, changing weather conditions and growing demand in countries like the US could culminate in a situation where the trees that make these bats could soon be in short supply. According to Ruggles, quality trees are becoming rarer since they grow faster with increasingly warm temperatures. Longer seasons lead to the trees growing up until November, so they grow more with more comprehensive grains.
However, it is essential to note that wider-grain bats aren't necessarily low-quality and require more use or "knocking-in" before they are on the same level of play as tight-grained bats.
© Copyright IBTimes 2025. All rights reserved.