Robots to 3D print gravity-defying steel bridge in mid-air over Amsterdam canal
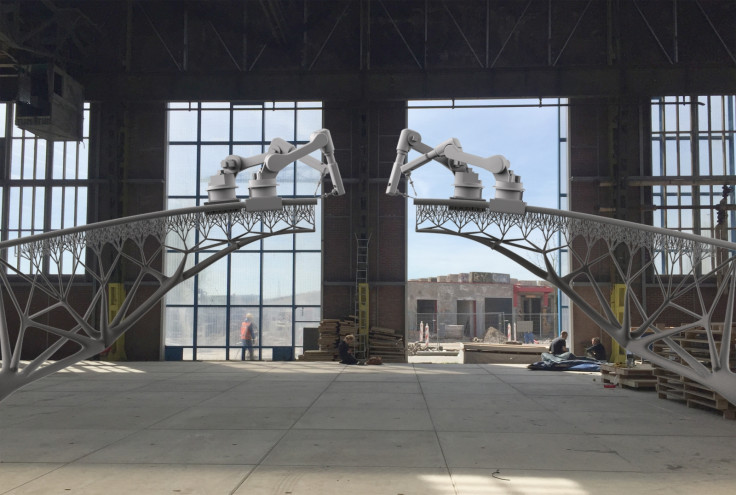
An ornate steel bridge will be built in mid-air over a canal in Amsterdam in 2015 using 3D printing and robots, and surprisingly it will not require support structures.
Dutch 3D printing R&D startup MX3D has invented a 3D printing technique whereby multi-axis industrial robots are able to print strong, complex structures anywhere without needing a print bed.
The multi-axis 3D printing technique works by 3D printing metal that melts, then solidifies within a second.
Aided by the geometry of the overall bridge design, the strength of the metal and support from the edge of the canal and the robot, the material is able to print horizontally without bending and falling into the water due to gravity.
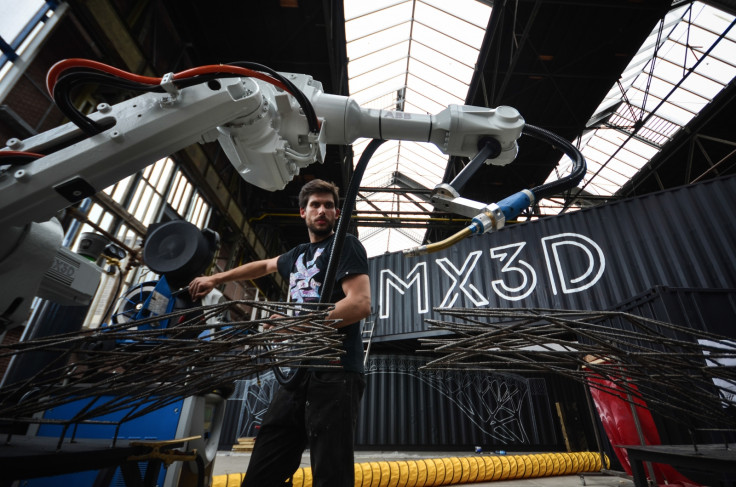
"We start with a piece of metal attached to the canal bank. The robots start from one side of the canal, they print their own support structure, so essentially it prints its own bridge. It stands on the floor of the bridge, 3D prints out more and keeps moving," MX3D's CTO Tim Geurtjens told IBTimes UK.
"We have the same physics as everyone else, but it looks like it's gravity-defying. We put a drop of metal, drop by drop at a time and it solidifies. But you could also print tubes, and then print layer over layer of tubes."
3D printed metal retains 90% of normal metal's strength
The robot arms are similar to those used in the car industry and they can print metals and plastics from single extruders, as well as combinations of the two materials together.
The 3D printed bridge project is a collaboration between MX3D, designer Joris Laarman, Autodesk, construction firm Heijmans and several other partners, including French welding specialists Air Liquide.
There could be concerns about how strong 3D printed metal is compared with traditionally welded metal but stress tests conducted by Delft University of Technology (TU Delft) proved MX3D's 3D printed steel retains 90% of the strength of normal stainless steel.
And by using software developed by MX3D, together with additional software by 3D modelling software firm Autodesk, the overall design of the bridge can be made to be much more efficient and feature a complex, ornate design that is as strong as a bridge built from stainless steel.
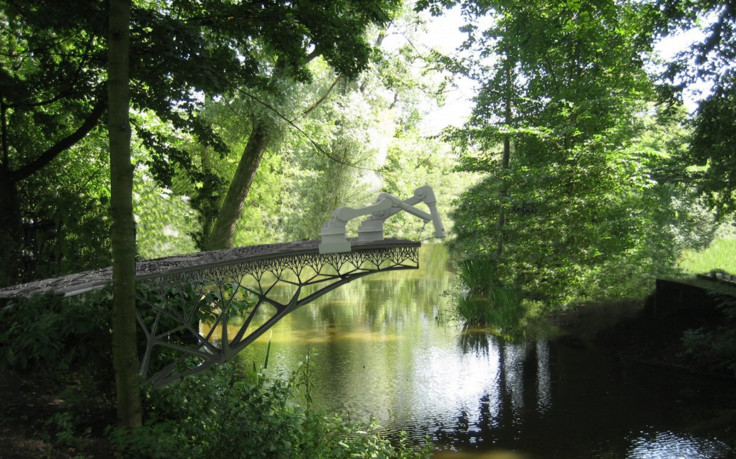
"Autodesk is working on a new topology optimisation software which goes further than most traditional optimisation software. It will take into account more parameters and constraints. If you incorporate those parameters into the design software, the whole process will be more efficient and it makes the bridge stronger," said Geurtjens.
A visitor centre will be opened in September so people can learn about the project, while the bridge will very likely take two to three months to be printed. However, MX3D is still developing its software and working with its partners to make sure the final bridge design is as strong, safe and efficient as possible, so the project will be completed by the end of 2017.
Changing how robots are programmed with additive manufacturing
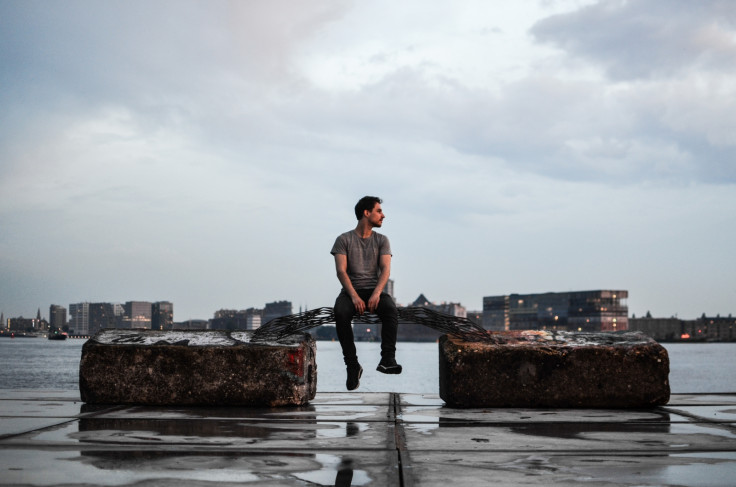
Discussions about where the bridge will be located are still ongoing with the City of Amsterdam but MX3D is aiming to place the bridge over an old canal near the city centre.
Commercialising its technology is definitely on the cards but for now, MX3D is focusing on software development and offering printing services to companies and artists, as well as building a development lab with TU Delft and Amsterdam Institute for Advanced Metropolitan Solutions that will open in the summer.
The robotic arms used by MX3D are provided by robotics firm ABB and in the future, MX3D hopes to be able to print other materials such as concrete and ceramics, and perhaps even with multiple extruders.
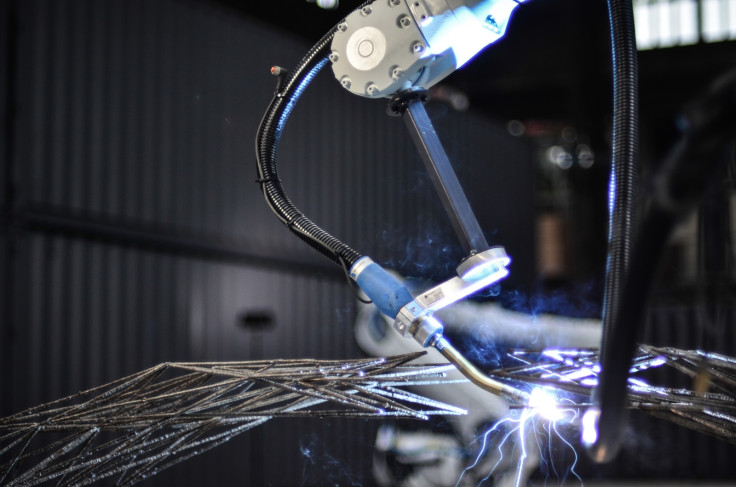
In fact, Geurtjens says MX3D's software could change the future of robotics. He said: "Our software translates CAD model software into welding strategies, and then translates that into the Rapid software used by ABB to tell the robot how to move.
"In almost all cases, robots are used in industry, programmed to do repetitive tasks like paint the car or weld specific parts. You execute it for years and years in a row after programming it once.
"Up until now with our project, no two pieces of information being related to the robots are ever the same, so everything we print is generative. This could change the future of robotics."
© Copyright IBTimes 2025. All rights reserved.