Airbus 3D prints entire aircraft to demonstrate the future of simplified aeroplane manufacturing
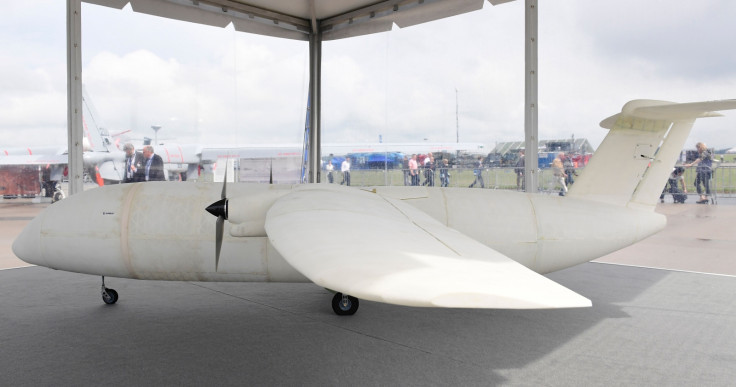
French aircraft manufacturer Airbus has showcased a mini plane constructed completely from 3D printing at the International Aerospace Exhibition and Air Show in Berlin (ILA Berlin Air Show 2016) in order to demonstrate what the future of aeroplane manufacturing will look like.
The Thor mini plane is windowless, weighs 21kg and is just under 13ft long. It is entirely 3D printed from polyamide and the only parts not 3D printed are the electrical components. Thor resembles a large white model aeroplane but is classified as a drone because it has to be autonomously manned.
"This is a test of what's possible with 3D printing technology," Detlev Konigorski, head of developing Thor at Airbus told AFP. "We want to see if we can speed up the development process by using 3D printing not just for individual parts but for an entire system."
Proving 3D printing's safety in aerospace could take a while
3D printing, also known as additive manufacturing, is a new technology that enables industries to manufacture materials much faster than the traditional injection moulding technique traditionally used. Today, 3D printing is being used more and more in healthcare and to rapidly prototype designs in manufacturing, but there is a great interest in using 3D printed components to speed up production of aircraft and space rockets.
However, at the moment only 3D printed plastic is approved for use in aircraft carrying humans as there are concerns that 3D printed metal is not yet as strong and safe as metal components manufactured in the traditional way.
A recent study by Carnegie Mellon University (CMU) analysing 3D printed titanium parts with deep X rays and found that there are significant flaws when titanium metal powders are sintered together as gas can become trapped in the resulting liquid layer, creating porous bubbles within the final solidified metal part.
Aerospace industry convinced of 3D printing's promise
Despite this, Airbus is currently testing how to 3D print an entire injection assembly for a jet engine, rather than manually assembling it from 270 individual pieces, and in May the manufacturer also filed a patent for a revolutionary new 3D printing process that would make it possible to print out an entire aircraft's exteriors in one go from multiple metals.
Other aerospace firms also see the huge potential additive manufacturing – Boeing is using 3D printing to create fuel nozzles, sensors and fan turbine blades for its high tech Boeing 777x line of huge passenger airliners, while Lockheed Martin-Boeing joint venture United Launch Alliance (ULA) is testing plastic 3D printed parts as an outer shell on its Atlas V rockets.
"With 3D printing, [the assembly] has just three parts," Alain Charmeau, head of Airbus Safran Launchers told AFP. "It brings big cost reductions on parts manufacturing."
© Copyright IBTimes 2025. All rights reserved.