BAE Systems launches UK centre to push 3D printing and VR to speed up aircraft manufacturing
BAE says 3D printing and virtual reality are helping improve production processes for the Eurofighter Typhoon.
British aerospace manufacturer BAE Systems is making a big push into 3D printing and virtual reality (VR) in order to drastically speed up the production times of military aircraft.
On 15 March BAE Systems opened the doors to its New Product and Process Development Centre (NPPDC) in Samlesbury, Lancashire for the first time. The centre will be focused on using 3D printing and VR to reduce costs and speed up manufacturing processes for several military aircraft, including the Eurofighter Typhoon and the BAE Systems Hawk.
3D printing – also known as additive manufacturing – is a technology that has been used by BAE Systems for the last two decades, due to its ability to enable rapid prototyping of new designs. However, the aerospace manufacturer is now ramping up reliance on the technology. In 2016, over 2,500 components were produced using 3D printing, which is a 20% increase over the last 12 months.
The argument for using 3D printing in aircraft manufacturing is that it is faster, cheaper and simpler. For example, the Environmental Control System (ECS) used in the Eurofighter Typhoon twin-engine canard-delta wing multirole fighter jet consists of nine individual components that have to be separately manufactured and then assembled before the system can be fitted onto the aircraft.
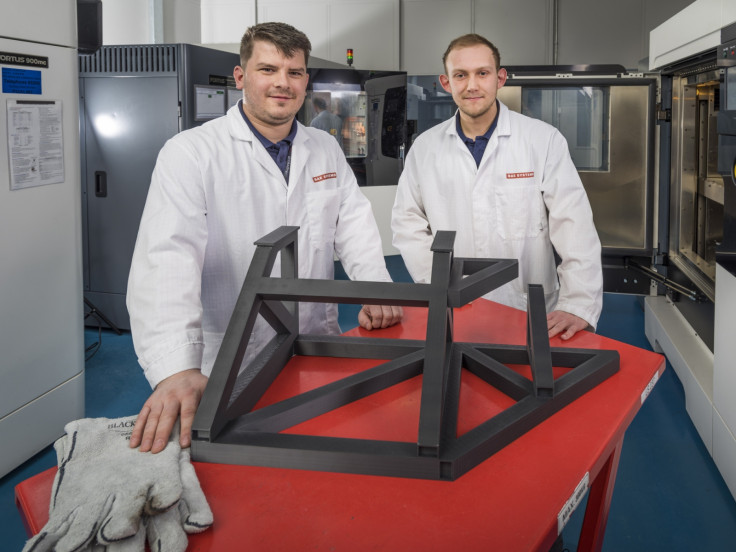
With 3D printing, the whole system can be 3D printed as one complete part, which compresses lead time by 75% while delivering cost savings of up to 57% compared to the traditional method of developing the system.
BAE says it is 3D printing parts out of Grade 2 Commercially Pure Titanium using Selective Laser Melting (SLM), as well as Flame Retardant Nylon, used in Selective Laser Sintering (SLS) – both materials that have been approved for use in aircrafts.
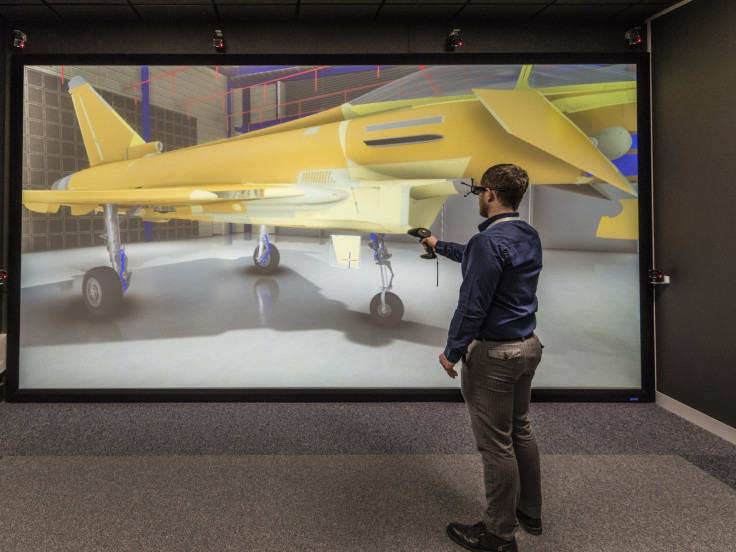
Rapid prototyping is a great way to visualise product designs without having to wait ages for the prototypes to be made using injection moulding, but BAE takes it a step further. Rather than print out multiple designs, why not visualise them first in virtual reality?
To that end, the new centre comes with a VR Suite where aerospace engineers can look at aircraft parts virtually in 3D, see how the parts would work and fit in with the rest of the aircraft and hopefully spot errors and problems even faster.
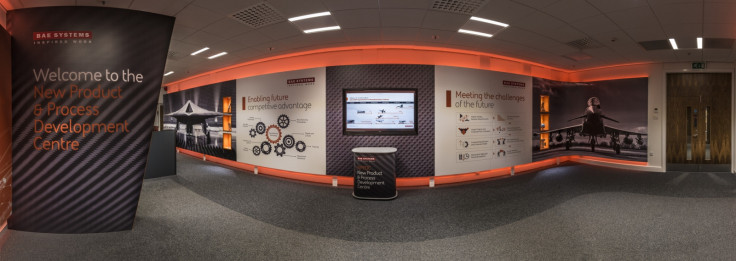
"We've got a ramping F-35 programme that demands a drum beat manufacturing system be put in place. We've also got.... Typhoons moving into the export marketplace, and it's about how do we respond to the challenges of those programmes," said John Dunston, head of the NPPDC at BAE Systems.
"Our raison d'être really is to establish a productionised suite of processes that we can then either deploy to a programme or run as a shared service within the facility, or... look at how we can support the industrialisation activities and potentially deploy solutions in Coventry in support of [land system] programmes."
© Copyright IBTimes 2025. All rights reserved.