MIT invents 'breakthrough' 3D printer that can print 10 different materials simultaneously
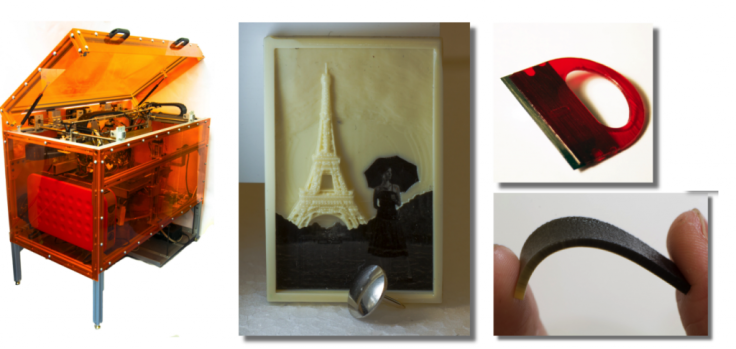
Researchers from MIT's Computer Science and Artificial Intelligence Laboratory (CSAIL) have made a breakthrough in the field of 3D printing, developing a 3D printer prototype that is able to print up to 10 different materials simultaneously onto a single object.
At the moment, most conventional 3D printers can only print out one material layer-by-layer at a time, whether it be plastic, metal, ceramics or wood, and users need to keep an eye on the printer as the print can easily go wrong.
Multi-material 3D printers do exist, and Stratasys launched the world's first multi-material full-colour 3D printer in January 2014 that is able to print objects out of rubber and plastic, but it costs up to $250,000 (£159,660) and still requires a great deal of human intervention in the printing process.
However MIT's new MultiFab 3D printer might have changed the game yet again by creating an all-in-one system costing $7,000 that can quickly print out multi-material, multi-component objects with a lot less hassle.
The open-access research paper, entitled: "MultiFab: A Machine Vision Assisted Platform for Multi-material 3D Printing" is available to read here.
How MultiFab works
First, a central computer is told what the user wants to create. While running the printing software, the computer receives views of what the printed object looks like, sent from a 3D scanner within the 3D printer, using a technology, known as machine vision.
In some up-market 3D printers, there are mechanical systems that move back and forth over the print, touching it constantly to feel whether each layer is being printed properly. However, machine vision is different – it is contactless, using the same scanning technology usually used by robots in industrial manufacturing processes.
The 3D geometry data sent by the scanner gives the 3D printer's computer the ability self-calibrate the machine and to self-correct any mistakes. The computer is then able to adjust the printing process and decide which materials need to be printed onto the object, for example, a circuit board.
But the user can also take specialised components and insert them into the machine, where they will then be added to the object, and the computer is clever enough to then continue printing around these added components to incorporate them into the final product.
"With MultiFab, we integrate these two worlds of traditional manufacturing with 3D printing, and by putting them together, we can make a whole range of new objects that we are not currently able to make today," said Javier Ramos, a research engineer with CSAIL and co-author of the research paper.
"Right now, 3D printers are focused on printing form and objects for prototype, but the Holy Grail would be to print out things that are fully functional right out of the printer, combining multiple materials with many properties."
Advanced electronics possible in the future

So far, the CSAIL researchers have succeeded in printing out LED lenses, a plastic blade holder containing a metal blade in it, and smartphone cases that print around the smartphone, but they see MultiFab being applied in the manufacturing of consumer electronics, medical imaging, microsensing and telecommunications.
The next step for the researchers will be to 3D print objects that include embedded motors and actuators. If the finished products were able to function, it could open up the possibilities of being able to 3D print advanced electronics, such as robots.
"Designers and engineers are used to designing with just one material, so the whole design paradigm will have to change. That's going to require new hardware and software, and we're going to have to change the way us engineers and designers think about design," said Ramos.
"Picture someone who sells electric wine-openers, but doesn't have $7,000 to buy a printer like this. In the future they could walk into a FedEx with a design and print out batches of their finished product at a reasonable price. For me, a practical use like that would be the ultimate dream."
© Copyright IBTimes 2025. All rights reserved.