Spider weaves electrically charged silk that can teach scientists about nano-scale filaments
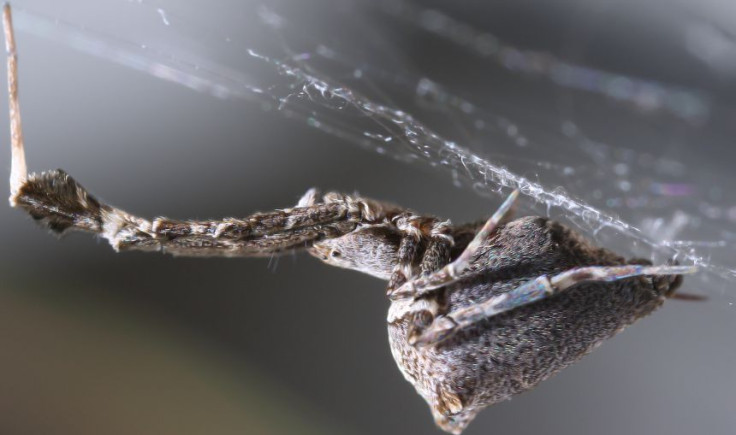
Scientists from Oxford University's zoology department are studying how a spider typically found in UK garden centres spins its webs, in order to understand how to manufacture ultra small yet ultra strong fibres.
Most spiders weave their webs out of silken strands that measure a few micrometres in thickness and use tiny blobs of glue to make the silk sticky in order to trap their prey.
However, the feather-legged lace weaver spider, also known as "Uloborus plumipes" or the "garden centre spider" is different.
She is able to spin incredibly long and strong silk fibres that are not only just a few nanometres thick (that's millionths of a millimetre), but also electrostatically charged to trap prey, similar to how a towel taken out of a dryer can attract and stick to other clothes.
The researchers have been trying to figure out how this spider is able to do it, and have detailed the process in a new paper entitled "Spiders spinning electrically charged nano-fibres" published in the journal Biology Letters.
Silk thread is produced from a spider's cribellar gland and in most spiders, the silk produced is completely intact. The scientists were surprised to see that when the silk emerged from Uloborus plumipes, it was in a liquid state.
In fact, this spider's cribellar gland consist of thousands of silk-producing units – tubes that average 500 nanometres in length which carry the silk raw material, and spigots that narrow to a diameter of around 50 nanometres where the silk emerges.
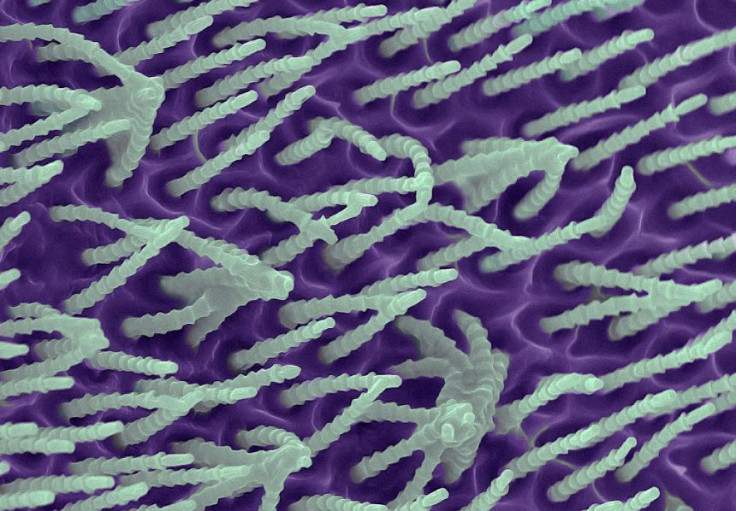
"Uloborus has unique cribellar glands, amongst the smallest silk glands of any spider, and it's these that yield the ultra-fine 'catching wool' of its prey capture thread," said Dr Katrin Kronenberger of Oxford University's Department of Zoology, the report's first author.
"The raw material, silk dope, is funnelled through exceptionally narrow and long ducts into tiny spinning nozzles or spigots. Importantly, the silk seems to form only just before it emerges at the uniquely-shaped spigots of this spider."
As the silk emerges from all these units in a liquid state, the spider yanks at it, causing the fibres to stretch and freeze into shape.
As the fibres in the thread stretch, they become very strong, and the spider then pulls the thread over a comb-like plate located on its hind legs, which gives the thread an electrostatic charge, and creates its wool-like appearance.
The spider's technique is not unlike the way flax is processed, whereby flax fibres are pulled through a metal comb, which parts the fibres and makes it easier for them to be spun into thread, which can then be woven into linen.
The polymer fibres produced today that go into synthetic materials usually have diameters of 10 micrometres or thicker. If synthetic filaments could be manufactured commercially at a super-small nano scale, then they could also be longer and stronger.
"Studying this spider is giving us valuable insights into how it creates nano-scale filaments," said Professor Vollrath.
"If we could reproduce its neat trick of electro-spinning nano-fibres we could pave the way for a highly versatile and efficient new kind of polymer processing technology."
© Copyright IBTimes 2025. All rights reserved.