What is a 'connected plant'? Honeywell's Jason Urso explains its ubiquitous industrial appeal
Underpinned by the Industrial Internet of Things, the concept is changing industrial and manufacturing processes in the digital age.
In step with our digital age, the industrial and manufacturing world is increasingly deploying automation and cutting edge technology to improve efficiency, predict issues with degrading equipment, forecast weather trends and train workers.
Underpinning it all is the Industrial Internet of Things or IIoT which has led to the dawn of the 'connected plant'.
In the simplest of terms, a connected plant is at the forefront of automation where parts and equipment of an industrial, petrochemical or manufacturing complex interact with each other to improve production processes, efficiencies and safety.
By linking the physical and virtual aspects of a plant, a modern connected facility has the ability to empower rapid decision-making like never before.
It can bring process areas, big data and human capital together to produce value in ways that were considered impossible a few years ago but are now deemed ubiquitous.
In the past, what's known as a distributed control system (DCS) served as the "brain" to a conventional plant centralising control, monitoring and reporting of the facility's assets for the operator.
In a connected plant, it is not just the brain or DCS that's available and accessible but also each "nerve ending" node, all interactive, all in real time and all reactive like never before.
Age of big data and bespoke solutions
Of course, for the likes of Honeywell Process Solutions (HPS), the multinational conglomerate's automation control solutions division, and its rivals – such simplistic definitions should already be consigned to the industrial jargon archives.
Jason Urso, chief technology officer of HPS, tells IBTimes UK, that solutions providers have already moved way beyond generic descriptions.
"For us, its about connecting big data to pools and knowledge so that we can deliver a very specific outcome for our customers. Those outcomes can include improving yield on products, reliability and people efficiency.
"Our connected plant mechanisms are bespoke solutions. We don't create a solution and go looking for customers whose problems it can match. We deliver an outcome-based service, with a guaranteed outcome, to accept a specific problem that exists within a customer's industrial facility."
Urso says the fourth industrial revolution or "Industry 4.0" is among us and many of HPS' customers - including some of the biggest refining and petrochemical companies - are feeling the impact.
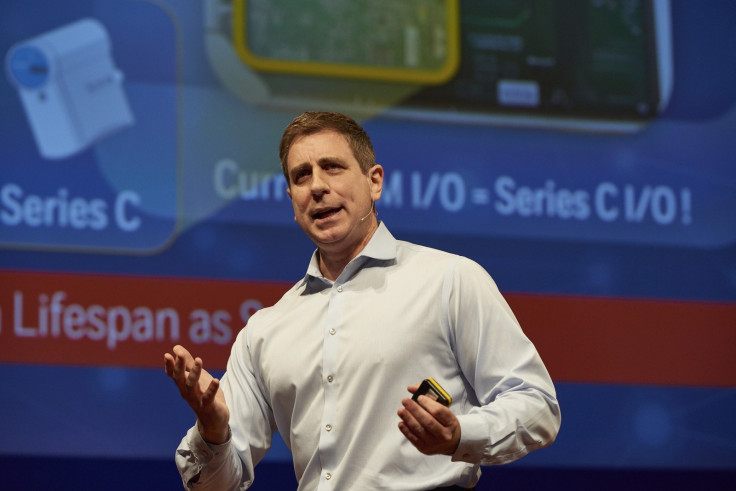
"As we look at existing customers, particularly downstream refining and petrochemical customers, they all have some similar needs.
"So for example, if a customer is operating a plant at capacity and needs additional capacity, by applying some of our advanced control and optimisation techniques, collecting data at the site, analysing it and driving a very specific control scheme at a particular plant, customers often see 3-4% extra throughput."
That saves millions of dollars the company might have otherwise needed to add extra capacity – all achieved by the power of data, software and analytics tools without having to go through a pretty substantial capital expenditure project.
"Simply put, customers get more bang for their buck in an era changing market dynamics."
Another issue could be plant maintenance and reliability. Nodes of a connected plant digitally identify upcoming issues and assist with keeping the production process going thereby reducing and avoiding unplanned downtime, and identify specific issues like plugging or fouling.
Affordable IIoT
Not only can connected plant operators get to the heart of the problem quicker; they can be more predictive, and preempt a process disruption.
Urso adds: "And lets be clear, digital IIoT solutions are not just for the high-end customers. The tools are ubiquitous, competitive, and tailored to differing price points for the industrial community. At HPS, by applying our expertise on a centralised basis, we are able to bring technology that was maybe out of reach for some in the past, but not anymore."
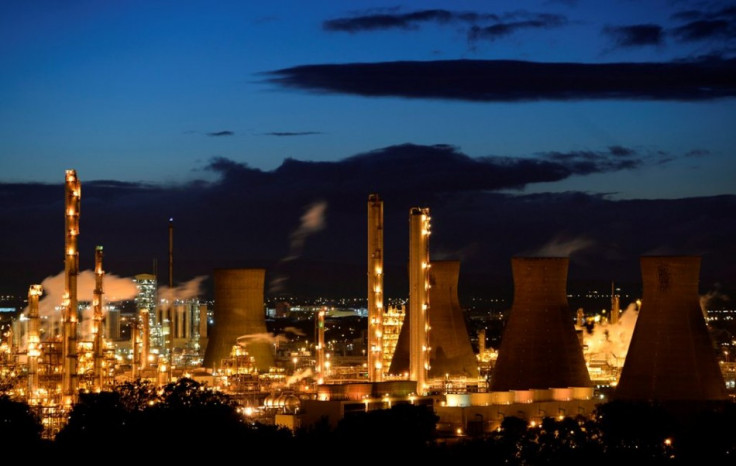
Then there are tools like virtual reality (VR) being deployed to train plant workers.
"Instead of the old way of shadow training on the job in a conventional plant, these days VR is deployed in training to provide an immersive mock-up of the environment in a world where technology is evolving fast, and training methods need to keep pace."
Urso admits that with every new innovation there are those that tend to be early adopters, yet others who take a more "wait and see" approach. Takers and naysayers of connected plants are no different.
"For HPS, connected plants form the present, not some distant future. The way we try to evolve the dialogue is by not just talking about the technology behind the story, but get more orientation around the outcome.
"And when you can sell an outcome to the customer and say we will go so far as to guarantee the outcome [for e.g. extra throughput or greater longevity between a turnaround cycle], then it becomes a little bit of an easier sell to the sceptics.
"It changes the nature of the discussion to the benefit, the outcome that's desirable for a customer, and then we can talk about some of the underlying technological elements that make it happen."
Keeping it safe and secure
Of course, with connectivity at the heart of a connected plant, cybersecurity spooks even the converted.
"Unfortunately, cyber risk will never go away. That's the nature of computing where there is always cyber risk. What we can do is dramatically reduce that exposure. I believe technologies are available today to ensure we are constantly ahead of the cybersecurity threats that are evolving every day," Urso says.
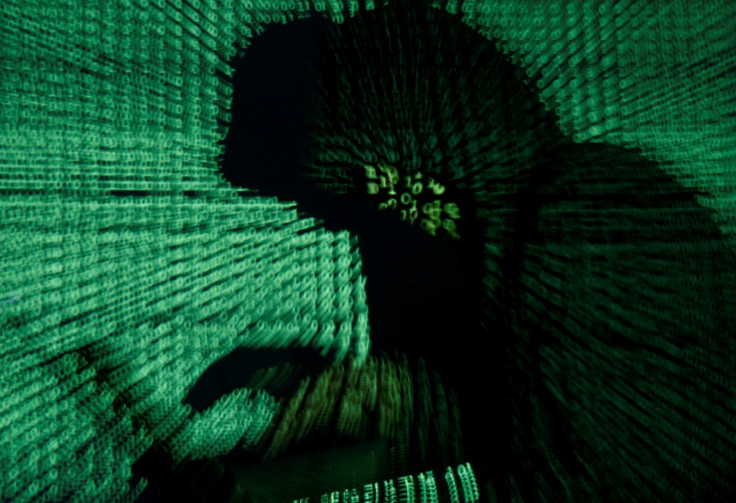
"But putting in place layers of protection in a connected plant is only one aspect. We need to make sure that security policies and procedures are in place, that people are trained to observe cybersecurity protocols.
"We're all about giving people tools – where risks and vulnerabilities exist within the organisation – but also about making people more risk aware. Sometimes attacks start with the simplest of slip-ups such using an infected USB. So training is crucial."
Ultimately, the technological premise coupled with improved outcomes would win the day, Urso says, adding that connected plants are part of the inexorable direction of travel for the industrial complex. "Industrial revolutions are about progress, and by their very nature connected plants represent a progressive leap in every aspect possible – outcome, safety, efficiency and reliability."