3D printing breakthrough: Heat-resistant ceramics for use in hypersonic jets now possible
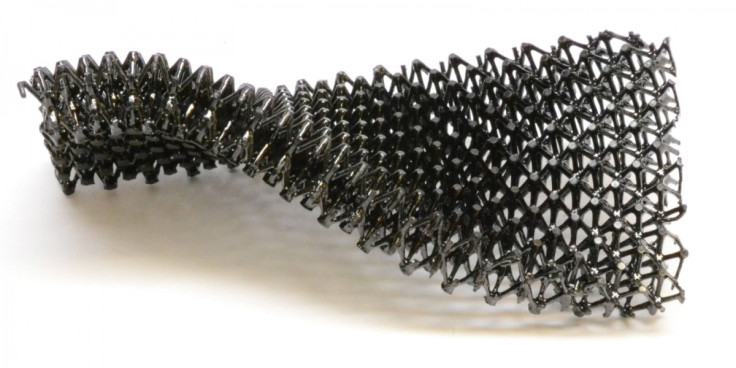
Darpa-funded engineers have found a way to create a heat-resistant ceramic material that can be 3D-printed and still retain its strength. This opens up the use of 3D printing in multiple applications in the aerospace industry, including building components for hypersonic jets and spacecraft.
Researchers from HRL Laboratories in Malibu, California have invented an incredibly strong ceramic polymer resin that can withstand temperatures of more than 1,700 degrees Celsius and be able to be moulded into complex shapes. At the moment, ceramic materials are not suitable for being 3D-printed as they require an incredibly high temperature before the particles will melt and fuse together properly, and currently, 3D-printing experiments have shown that the resulting ceramics often tend to crack or have fractures in the material.
Rising interest in using 3D printing in aerospace
3D printing, also known as additive manufacturing, is a new technology that enables industries to manufacture materials much faster than the traditional injection moulding technique traditionally used. Today, 3D printing is being used more and more in healthcare and to rapidly prototype designs in manufacturing, but in the fields of aerospace and defence, 3D-printed metals and ceramics are still not safe enough to guarantee no structural weaknesses when planes are sent up into the air.
However, being able to 3D print components for the aerospace industry has myriad benefits, and in April 2015, United Launch Alliance (ULA, a joint venture between Boeing and Lockheed Martin) told IBTimes UK that 3D-printing rocket components out of Ultem 9085 FDM thermoplastic material instead of using traditional methods is saving ULA up to $1m (£680,000) a year.
Making 3D-printed ceramics strong and durable
Ceramic 3D printers already exist today, but they make use of Fused Deposition Modelling (FDM) technology wherein objects are printed by the 3D printer's nozzle, laying down material layer by layer until the object is fully crafted.
While this is fine if you're just making an ornament, the material would need to be far stronger if used to hold an aircraft or spacecraft together in the face of aeroheating, where the outsides of space rockets and jets flying at incredibly fast speeds experience heat from friction.
The researchers created a new type of ceramic resin, and they found that if they used another popular 3D-printing technique known as stereolithography – whereby a laser beam is used to build structures layer by layer from a liquid polymer – making complex 3D structures would be possible. And once printed, the material could then be heated to turn it into incredibly strong ceramics.
Darpa dreaming of a powerful heat shield
The 3D-printed material could be printed to create large, lightweight lattice structures that would be suitable for building heat-resistant panels for aeroplanes and spacecraft, as well as smaller components for use in jet engines, and HRL Laboratories says that its ceramic lattice structures are 10 times stronger than commercially available ceramic foams.
Darpa, which funded the research, is hoping that the new ceramic polymer can be used to develop a ceramic aeroshell shield that can protect spacecraft and hypersonic aircraft from heat, pressure and debris, according to MIT Technology Review.
Although they withstand heat just fine, ceramic foams available today have poor mechanical properties meaning they are unsuitable for use in load-bearing structures.
The research, entitled 'Additive manufacturing of polymer-derived ceramics', is published in the journal Science.
© Copyright IBTimes 2025. All rights reserved.