ETH Zurich develops nanodrip 3D printing technique to make touchscreens more responsive
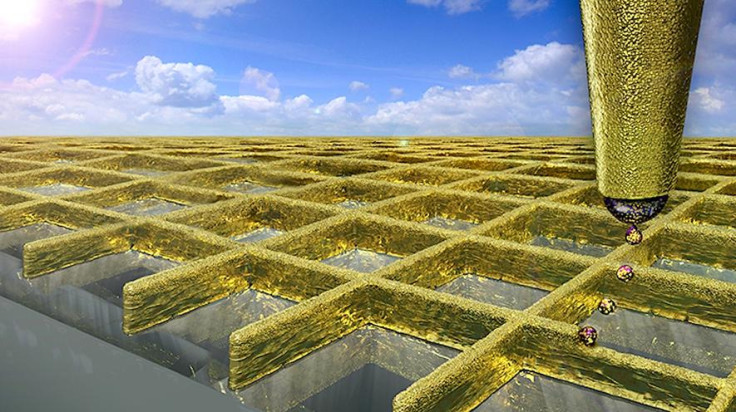
Scientists from ETH Zurich has pioneered a 3D printing process that makes it possible to manufacture transparent electrodes to make touchscreens far more responsive than they are today.
In order to make any glass touchscreen responsive, such as those used on smartphones and tablets, transparent electrodes need to be applied to the glass so the device or machine can detect exactly where a finger has touched it.
But what if you could make touchscreens lightning fast in terms of responsiveness? To achieve this, researchers from ETH Zurich used 3D printing techniques to create a special type of electrohydrodynamic ink-jet printing whereby tiny drops of gold are printed out to form ultra-fine gold walls that gradually build up to form a whole grid of nanowalls.
These nanowalls create the transparent electrode and they are so thin that they can barely be seen by the naked eye and are far more transparent and conductive than the touchscreen electrodes made today out of indium tin oxide.
The researchers say the more transparent the electrodes, the better the screen quality, and the more conductive they are, the more quickly the touchscreen will pick up finger movements.
Gold electrodes beat indium tin oxide for responsiveness
"Indium tin oxide is used because the material has a relatively high degree of transparency and the production of thin layers has been well researched, but it is only moderately conductive," said Patrik Rohner, a PhD student in the team.
So in order to make their electrodes more conductive, the researchers opted for gold and silver, which conduct electricity much better, but the shortfall is these metals are not transparent, so the scientists had to look at using much thinner amounts of the metals to construct a grid with walls that were only 80 to 500 nanometres in thickness.
To build the grid from such tiny metal walls, the researchers used a 3D printing process called Nanodrip that they invented in 2013. The process involves using inks made from metal nanoparticles in a solvent. An electrical field draws out super tiny droplets of metallic ink out of a glass capillary, which functions as the print head, and on the printbed, the solvent evaporates quickly so tiny walls of metal are built up drop by drop.
3D printing much smaller structures now possible
ETC Zurich says its 3D printing method is special because it enables tiny structures to be printed, since the droplets that come out of the glass capillary are about 10 times smaller than the aperture itself.
"Imagine a water drop hanging from a tap that is turned off. And now imagine that another tiny droplet is hanging from this drop – we are only printing the tiny droplet," said Dimos Poulikakos, professor of thermodynamics at ETH Zurich.
The scientists next need to upscale the printing process so it can be implemented on an industrial scale, and they believe the technology could be hugely useful and cost effective to print these tiny transparent gold electrodes compared to the production process used today for indium tin oxide electrodes. The technology could also be used in solar cells to harness even more electricity, as well as to further the development of curved OLED displays.
© Copyright IBTimes 2025. All rights reserved.